With the development of LED technology, the power of a single LED continues to increase, and its reliability is closely related to heat dissipation; in order to solve the problem of heat dissipation of high-power LEDs, copper-clad aluminum entry sheet PCBs have been widely used in the field of LED strips. For example, aluminum entry sheet PCBs carry High power LEDs are used in LCD TVs.
Structure of Aluminum entry sheet PCB for LED TV
Conductive layer: the main material is copper foil, the thickness of copper foil is 1 oz-6 oz and can be customized, and 1 oz is generally used in the light bar industry;
Insulation layer: the main materials are phenolic resin (glass fiber cloth) and film, the thickness is generally 3-6mil and can be customized; the light bar industry generally uses 4-5mil products;
Metal layer: The main material is aluminum plate (1 series, 5 series, etc.), the thickness is 0.4mm ~ 2.0mm and the thickness can be customized.
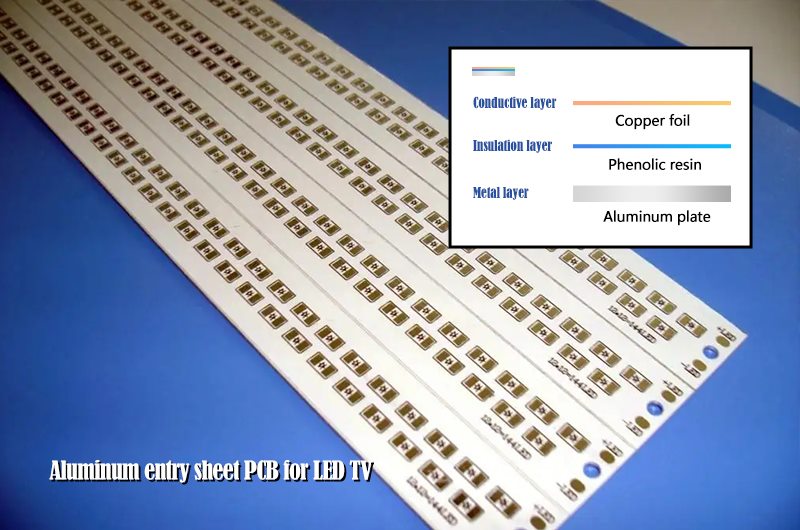
Aluminum entry sheet PCB for LED TV
Aluminum entry sheet PCB has good thermal conductivity and heat dissipation performance, and the breakdown voltage of large plates in insulation can basically reach AC: 3KV, DC: 4KV,
However, the insulation performance is greatly attenuated after processing into a finished PCB; at the same time, because the insulation thickness between the copper foil and the aluminum substrate is only 75-150um thick, the capacitance effect is also more obvious than that of the FR4 sheet.
In addition, due to the insulating layer between the copper foil and the aluminum entry sheet, a capacitor effect is formed; when the aluminum base surface of the aluminum entry sheet light bar is in contact with the backplane, the equivalent capacitance is superimposed into the corresponding driving circuit, especially when the LED driving belt When there is a MOS dimming circuit, the distributed capacitance will generate a corresponding pulse current. When the pulse current is large to a certain extent, it may cause corresponding backlight drive protection and LED high current damage.
In order to reduce the influence of distributed capacitance on the circuit of the whole machine, the following points should be paid attention to when designing the light bar with aluminum entry sheet:
1) Reduce the capacitance value of the distributed capacitance of the light bar; -- select a suitable dielectric constant plate and reduce the copper foil area;
2) The LED- in the light bar trace should be as short as possible, and the LED+ can be extended to reduce the influence of distributed capacitance on the drive;
3) When the driver end meets the performance requirements, the MOS solution without dimming is preferred;
4) If the dimming MOS solution is used, the equivalent capacitance value of the light bar is provided by the light bar in the early stage of development, and the driver end is designed with tolerance to ensure that the driver end has enough design margin for the aluminum-based distributed capacitance so as not to generate pulse current. or pulse current within specifications.
Design of aluminum entry sheet PCB for LED TV
1. Perfect wiring design:
1) The distance between the traces follows the following principles: the distance between the direct-type aluminum substrate trace and the edge of the board is greater than 1.5mm (more than 1mm in special cases);
2) The LED- is required to be short, and the width of the trace is reduced outside the range of 10mm to 20mm from the +- end of the LED pin to reduce the distributed capacitance and the probability of poor insulation between the copper foil and the aluminum base.
2 Optimization of the scheme design
1) For the aluminum entry sheet light bar solution, the single-channel driving voltage shall not be higher than 150V;
2) Evaluate the power drive end and seek new drive solutions, which can protect the poor insulation of the aluminum entry sheet in time;
3) The heat dissipation design requires that the aluminum substrate light bar must also meet the temperature rise requirements when it does not contact the backplane (suspended state);
4) Thicken the insulating layer to 150um aluminum entry sheet.