COB mirror aluminum entry sheet is mostly used in LED products, and the important characteristic of LED products is high reflection rate. COB packaging is to package the chip directly on the metal substrate and dissipate heat directly through the substrate. The conventional COB mirror aluminum entry sheet processing method is CNC processing, that is, the aluminum substrate is directly milled to the aluminum substrate through a milling machine to form a "COB". The uneven aluminum surface is reflected in the form of scattering, which is easy to lead to very low overall reflectance, so it is difficult to meet the quality requirements of LED products. The reflective rate of mirror aluminum plate can reach more than 95%. If mirror aluminum is directly used as the reflective surface of cob packaging, it will achieve ideal reflective effect Therefore, COB mirror aluminum entry sheet has become a hot product in the heat dissipation substrate market in recent years.
Aluminum profile for COB mirror aluminum entry sheet for LED
The aluminum models used for conventional aluminum entry sheet are 1050, 5052 and 6061 alloys. Through the comparison of the processing properties of these three aluminum materials, the processing surfaces of 1050 and 5052 aluminum materials are smooth, free of knife marks and good gloss. Therefore, 1050 and 5052 aluminum materials need to be selected for mirror polishing aluminum materials.
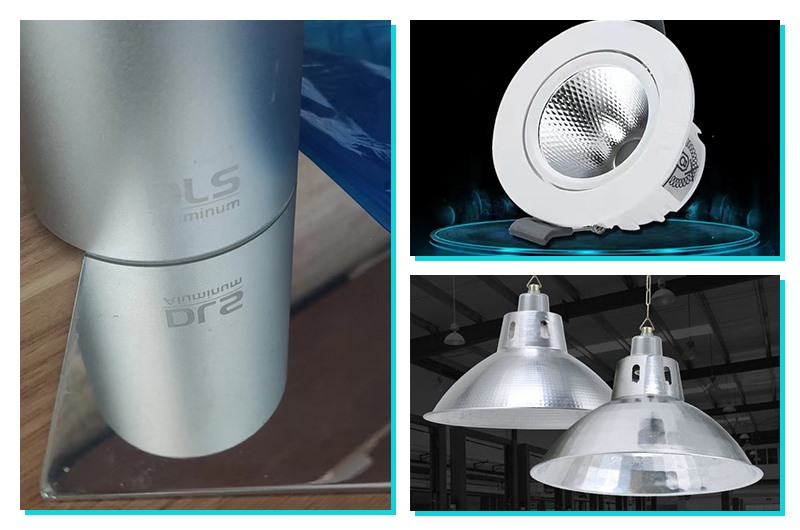
Chemical composition of 1050 and 5052 PCB aluminum entry sheet
Alloy | Si | Fe | Cu | Mn | Mg | Cr | Ni | Zn | V | Ti | Zr | Other | AL | |
single | total | |||||||||||||
1050 | 0.25 | 0.40 | 0.05 | 0.05 | 0.05 | - | - | 0.05 | 0.05 | 0.03 | - | 0.03 | - | 99.50 |
5052 | 0.25 | 0.40 | 0.10 | 0.10 |
2.2 -2.8 |
0.15 -0.35 |
- | 0.10 | - | 0.05 | 0.15 | - | - | Remainder |
Production process of COB mirror aluminum entry sheet for LED
After ultra-precision machining, aluminum can produce mirror effect. When parallel light shines on a smooth surface, the reflected light is parallel. This reflection is called "mirror reflection". The wick is pasted on the aluminum surface, the bottom of the concave cup is a smooth surface, and the angle of the concave cup wall is 45 °. The reflected light energy will produce parallel and vertical reflection, which can make the brightness of the wick more obvious and parallel and vertical emission, and increase the luminous rate. Aluminum cob concave cup bottom requires a plane with nano surface roughness. Concave convex problems are not allowed in the plane. If there are concave convex problems, parallel light will shine on the uneven surface, and the reflected light will shine in all directions. This reflection is called "diffuse reflection", which makes the reflection effect poor. At present, mirror milling and polishing technology is mainly used for batch processing of mirror aluminum. Mirror milling is made by vertical cutting for CNC machining center. Pictures and processing points can be selected at will. It mainly processes strange shapes, concave convex parts, motors, etc., which is suitable for the processing requirements of concave cups of cob aluminum substrate. The plane smoothness of diamond single crystal tool is particularly excellent, without any tool trace, and the mirror effect is good after machining. The use of cutting oil in mirror polishing can reduce the cutting rate of the surface and maintain the smooth brightness of the surface. During chip oil processing, control the speed, not too fast, otherwise it will cause fire problems. The larger the runout and swing of the spindle of the milling machine, the problem of knife marks will occur in the mirror machining of aluminum materials, which will affect the gloss of the surface; The runout and swing of the main shaft are small, and the aluminum mirror processing effect is good.