LEDs have been widely used in display, lighting, transportation, electronic devices and other industries due to their advantages of small size, low power consumption, long service life and environmental protection. At present, the input power of relatively mature commercialized high-power LEDs is generally 1W, the chip area is 1mm×1mm, and the heat flux density reaches 100W/cm2. With the development of LED to high power and high brightness, its heat dissipation problem is becoming more and more prominent, and it must be solved from the aspects of thermal conductive material and heat dissipation structure.
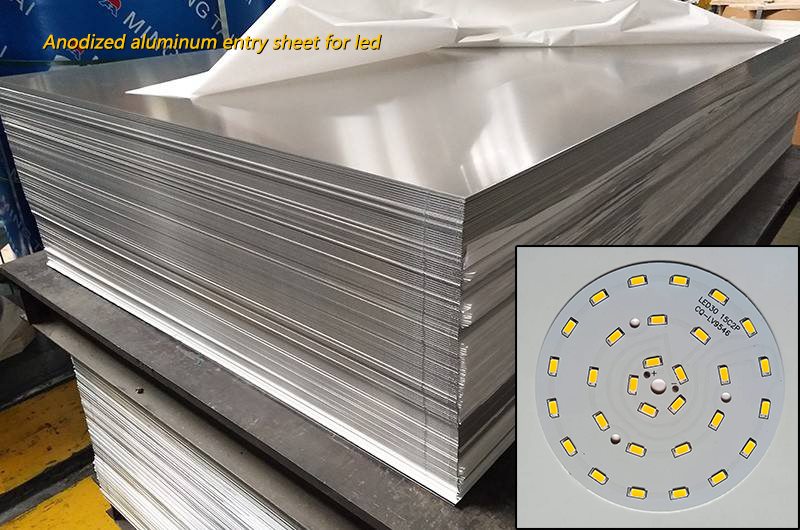
The heat dissipation substrate is one of the effective means to solve the heat dissipation problem of high-power LEDs. Substrate materials for high-power LEDs must have high thermal conductivity, high stability, high electrical insulation properties, a thermal expansion coefficient similar to that of chips, as well as flatness and high strength. The thermal conductivity of the alumina film produced by ion micro-arc oxidation is about 2W/(m·K), which is much higher than the thermal diffusivity of general thermally conductive resins and polymer PCBs. When the film thickness is 40μm and 20μm, the thermal resistance is 11.3K/W and 9.1K/W respectively. Therefore, it is very suitable and advantageous to apply alumina substrate to LED heat dissipation.
Production process of anodized aluminum entry sheet for led:
5052 aluminum plate → degreasing → cleaning → alkali corrosion → cleaning → gloss treatment → cleaning → anodizing → cleaning → drying.
Advantages of anodized aluminum entry sheet for led:
1. The thermal conductivity is very high, generally ranging from 30W to 50W. The thinner the thickness of the plate, the better the thermal conductivity, and the thicker the plate, the lower the thermal conductivity. But the overall thermal conductivity is 100 times or more than that of ordinary PCBs.
2. Strong stress, stable shape; high strength, high thermal conductivity, high insulation; strong bonding force, anti-corrosion.
3. Good thermal cycle performance, the number of cycles is up to 50,000 times, and the reliability is high.
4. Like the PCB board (or IMS substrate), it can etch the structure of various patterns; no pollution and no pollution.
5. The operating temperature is -55℃~850℃; the thermal expansion coefficient is close to that of silicon, which simplifies the production process of the power module.