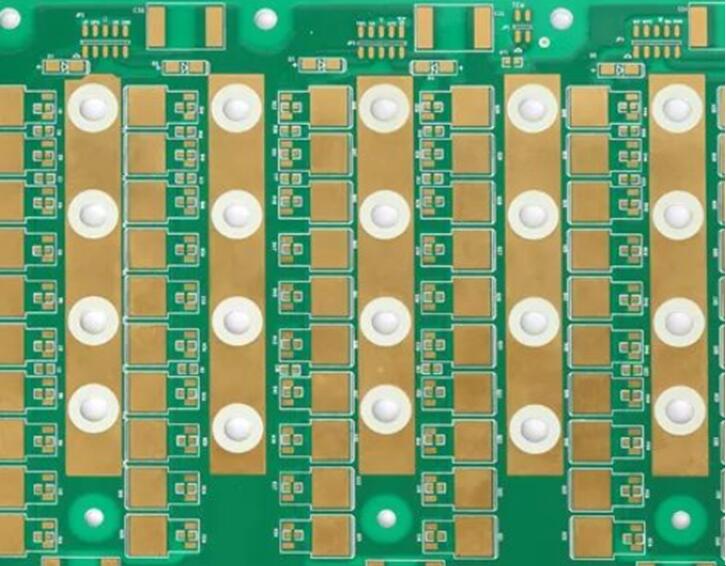
In the "hybrid" IMS structure, the "sub components" of the non thermal material are treated independently, and then amitron hybrid IMS PCBs are bonded to the aluminum substrate with thermal materials. The most common structure is a two-layer or four layer sub assembly made of traditional FR-4. Bonding this layer to an aluminum substrate with thermoelectric medium can help heat dissipation, improve rigidity and act as a shield. Other benefits include:
1. It's cheaper than building all thermal conductive materials.
2. Provides better thermal performance than standard FR-4 products.
3. Expensive radiators and associated assembly steps can be eliminated.
4. It can be used in RF applications requiring RF loss characteristics of PTFE surface layer.
5. The use of assembly windows in aluminum to accommodate through-hole assemblies allows connectors and cables to pass connectors through the substrate while welding fillets to produce a seal without the need for special gaskets or other expensive adapters.