In electronic equipment, small power tools, home appliances, children's toys and other electronic terminal products, a large amount of heat will be generated when the high-power devices on the printed board work. In order to solve this problem, according to the existing process flow, the process is improved step by step by brushing solder paste with steel mesh, making welding tooling, etc. In order to improve the old assembly method and welding process, improve the welding quality and work efficiency of products.
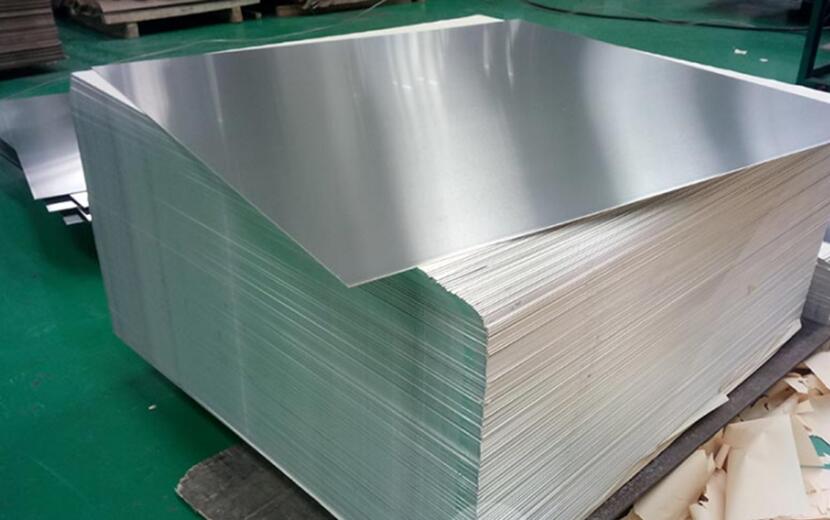
Brush method for welding of PCB and aluminum entry sheet
For the printing problem, we plan to use stencil printing. The first thing to consider is the design requirements of the stencil. Different from ordinary circuit boards, the aluminum substrate in the welding combination of the printed circuit board and the aluminum substrate needs to be scraped with solder paste on a large area (the scraping area is as high as 80% or more). Because the scraping area is too large and the surface is tin-plated (very smooth), it is easy to cause the solder paste to fall off due to weak adhesion when scraping the solder paste on the pad. For the above problems that are prone to occur, a mesh surface composed of many circular holes with a diameter of 1mm is designed to replace the large-area scraping surface opening, which makes the solder paste easier to demold and form. After the stencil is made, the automatic machine screen printing is carried out, which effectively controls the brushing part and the thickness of the solder paste, and it is formed at one time (see Figure 2), and the adhesion is good. , Reserve screw holes, and leave a border without solder paste around the tile to prevent short circuits caused by excessive solder paste. The thickness is uniform, which greatly improves the assembly efficiency and quality.
Tooling for welding of PCB and aluminum entry sheet
In the welding combination of the printed board and the aluminum substrate, the aluminum substrate and the printed board are required to be closely welded. The main purpose is to quickly transfer the large amount of heat generated by the high-power diodes on the printed board to the metal aluminum substrate through the ceramic plate. up and dissipate it effectively. Due to the large number of high-power diodes on the printed board, a large area of seamless connection is required to ensure the overall heat dissipation effect. When there is no welding tooling, after the worker finishes applying the solder paste, in order to ensure that the aluminum substrate and the printed board can be closely welded, the mounting holes on the edge of the board should be used to install screws for temporary fastening, and the printed board and the aluminum plate should be manually tightened. After 10 mounting screws between the substrates, clamp the printed board and the aluminum substrate with steel clips, and put them into a reflow oven for soldering.