As the substrate material in the manufacture of printed circuit boards, aluminum-based copper clad laminates mainly play the role of interconnection, insulation and support for printed circuit boards, and have great effects on the transmission speed, energy loss and characteristic impedance of signals in the circuit. The performance, quality, processability in manufacturing, manufacturing level, manufacturing cost, and long-term reliability and stability of printed circuit boards largely depend on aluminum-based copper clad laminates. Copper-clad aluminum substrates are widely used in emerging LED lamps, microelectronics and other industries due to their optimal cost performance, excellent electrical performance, heat dissipation, electromagnetic shielding, and high withstand voltage.
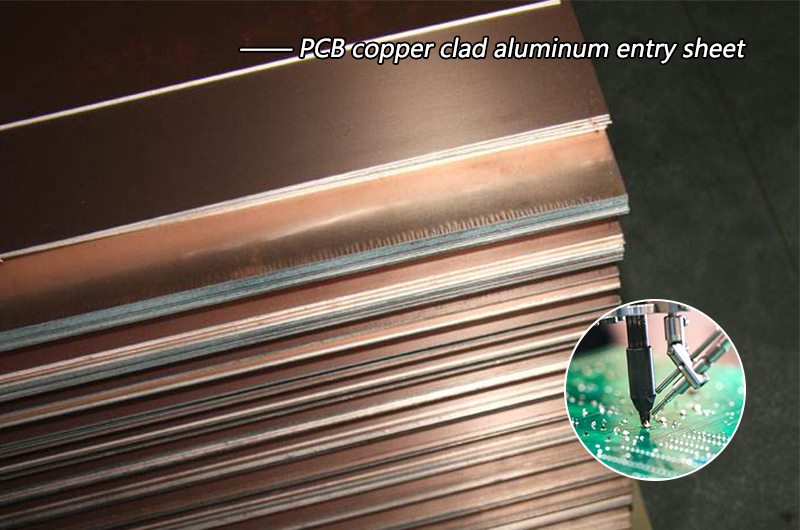
Composition of PCB copper clad aluminum entry sheet
Aluminum-based copper clad laminate is a kind of plate material made of electronic glass fiber cloth or other reinforcing materials impregnated with resin, single resin, etc. as an insulating adhesive layer, one or both sides are covered with copper foil and hot pressed. The aluminum-based copper clad laminate is generally composed of a single-layer structure, which is a circuit layer (copper foil), an insulating layer and a metal base layer. For high-end use, there are also double-sided designs with a structure of circuit layer, insulating layer, aluminum base, insulating layer, and circuit layer. Very few applications are multi-layer boards, which can be made by laminating ordinary multi-layer boards with insulating layers and aluminum bases.
Three types of PCB copper clad aluminum entry sheet
1. The thermal conductivity is relatively low with a thermal conductivity of 1.0;
2. The medium thermal conductivity with thermal conductivity of 1.5;
3. The highest thermal conductivity is above 2.0.
Advantages of PCB copper clad aluminum entry sheet
(1) The quality of the power module can be greatly reduced to meet the needs of the lightweight development of the module, while the heat dissipation copper base plate and ceramic substrate of the traditional module are denser and heavier;
(2) The power module packaging can be made simpler, eliminating the need for ceramic substrates and heat-dissipating copper backplane screen printing and other processes, greatly shortening the production cycle, and facilitating the automated production of modules;
(3) It has good thermal conductivity and dielectric properties;
(4) The price of copper-clad aluminum substrate is much lower than that of heat-dissipating copper base plate and DBC ceramic substrate, which can greatly reduce the production cost of power modules.